Bag it up and make it quick!
PRESSRELEASE: In the latest technology innovation from members of TMAS (the Swedish textile machinery association), ACG Kinna and ACG Nyström have teamed up with Juki Corporation – the world’s leading sewing machine manufacturer – in the development of a new automated line concept that can considerably speed up the production of finished filter bags.
PRESSRELEASE: 200210
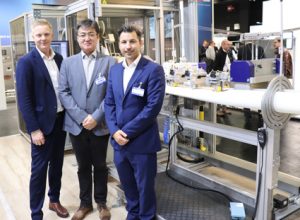
Pictured (left to right) are ACG Nyström Vice-President Thomas Arvidsson, Masanori Awasaki, President of Juki Central Europe and Christian Moore, CEO of ACG Kinna
Woven or nonwoven filter bags employed in a wide range of industrial processes may be under the radar as products, but they represent a pretty significant percentage of technical textiles production.
According to a recent report from BCC research, a leading US analyst covering this sector, industrial filtration represented a $555 million market in 2019 and some of the key areas where such filter bags are employed include:
- Metal fabrication, with effective filtration required for manual and automated welding, thermal cutting, blasting and machining, especially for coolant filtration.
- The process and energy industries, including foundries, smelters, incinerators, asphalt works and energy production plants.
- Other key manufacturing fields – often where dust is generated – including the production of timber, textiles, composites, waste handling and minerals, in addition to chemicals, food production, pharmaceuticals, electronics and agriculture.
As an example of the scale of this industry and the high volumes of fabrics involved, one supplier recently received a single order for 30,000 filter bags to be used for flue gas cleaning at the Estonian Eesti Power Plant – the biggest oil shale fired power plant in the world. The bags can be anywhere up to eight metres in length and frequently have to be replaced.
Line integration
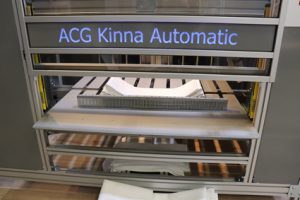
The SFL-2000 is the result of a four-year development project between Juki Central Europe and the two ACG companies.
The new SFL-2000 line is the result of a four-year development project between Juki Central Europe, headquartered in Poland, and the two ACG companies.
It is capable of handling a wide range of different filter media, and as an all-in-one solution, can produce high quality and accurate seams to predefined parameters, with optional modules allowing for customised constructions.
“The line can achieve sewing speeds of ten metres a minute with all kinds of fold, overlap and stitched seam, and up to 20 metres per minute with welded bags in widths of up to a metre,” says Christian Moore, CEO at ACG Kinna. “The unique selling point is that it build all sewing, welding and taping option into one flexible line to ensure less stops, and more importantly, quicker stops between changed of material, dimensions or joining options. This puts more money into the pockets of our customers.”
“This type of automation is the way forward, not just for filtration, but for all industries,” adds Masanori Awasaki, President of Juki Central Europe. “At Juki, our main technologies are for garment manufacturing, but we are also widely involved in the technical textiles field and this line integration concept is moving production on to the next level of efficiency.”
Joining options
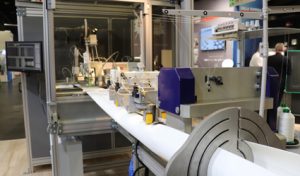
The line is available in three versions – the SFL-2000S for sewn seams, the SFL-2000-W and the SFL-2000WS employing both joining technologies.
The line is available in three versions – the SFL-2000S for sewn seams, the SFL-2000-W for welded alternatives and the SFL-2000WS employing both joining technologies.
The standard version of these lines has a single media roll feeder as standard, but as an option, a second can be added, with a Juki MO-6903G overlock head joining two separate materials together in continuous production, without any slow-down of the machine.
A custom pre-folding system creates the tubular form of the filter bag and the overlap just prior to the Juki sewing and welding units.
“The quality control system at this point employs three cameras inspecting and steering every parameter – the bag width and the width of the overlap, as well as seam accuracy – right down to the length of each stitch,” explains Christian Moore.” Three-axis positioning of the Juki modules ensures the seams are perfectly centred for precision consistency.”
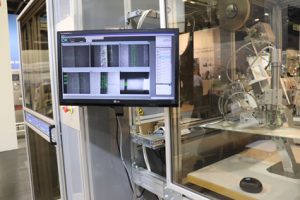
A quality control system employs three cameras inspecting and steering every parameter of production.
The bag is then conveyed to the cutting and printing unit.
“An inkjet printer is a further option at this stage, for the addition of QR and bar codes, and/or logos, and a buffer system of up to 1.5 metres prevents any stoppages as this is taking place prior to cutting,” adds ACG Nyström Vice-President Thomas Arvidsson.
“I continue to be surprised by the many fields of industry our TMAS members serve,” says TMAS Secretary General Therese Premler-Andersson. “The innovations from our companies during 2019 were far-ranging and characterised by an advanced grasp of Industry 4.0 automation techniques and the need for more sustainable processing methods that is being demanded by their customers. There will be much more of this to come in 2020 and beyond.”
Download the pressrelease (word): Bag it up and make it quick! Kinna Automatic
Read more about Kinna Automatic here!
For further information please contact:
Therese Premler Andersson, TMAS
Box 5510, 114 85 Stockholm,
Sweden
Phone: +46 8-782 08 50 | E-mail: tmas@tebab.com
www.tmas.com